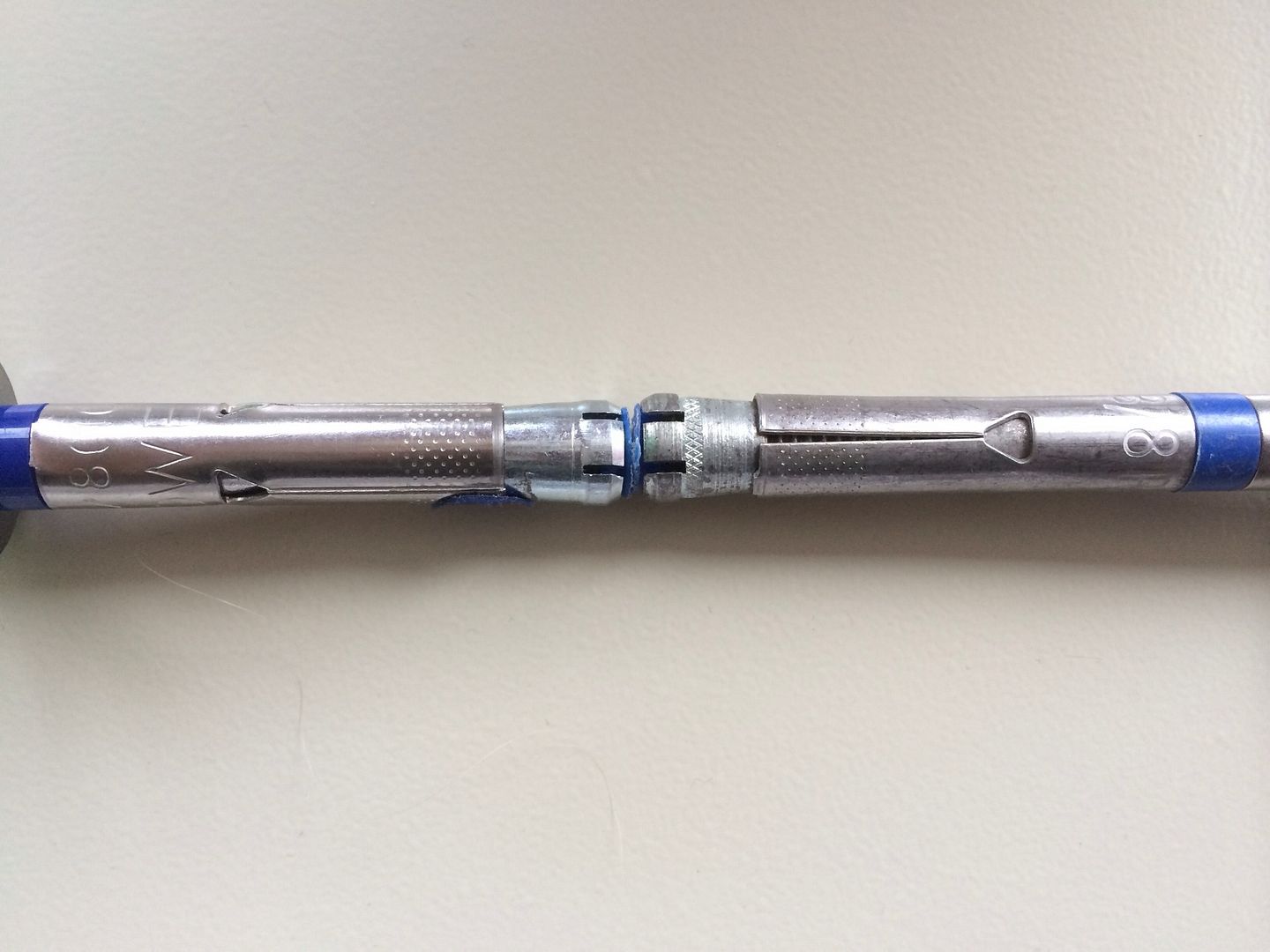
I knew I should have gone to school for mechanical engineering instead of Geology.
I’m not going back to grad school. I worked enough with engineers at Toyota.
I agree that the design is a problem.
The old bolt in Bruce’s pic has some knurling on the cone and the cone appears to have bigger slits. Both of the cones have a little bump-up in diameter just before the slits. What is the purpose of this bump? Is that the stop point for the cone entering the sleeve?
The description from Powers for how this bolt operates/tightens/expands reads as follows: Expansion occurs at two locations within the drilled hole. First, the cone is pulled into the large triple-tined expansion sleeve, developing a mid-level compression force. Further turning causes the threaded bolt to advance into the threads of the expander cone, forcing its four sections outward. This action engages the base material deep in the anchor hole, greatly increasing the holding power of the Power-Bolt. The bolt and cone remain locked together which prevents loosening under vibratory conditions.
Isn’t this the problem? If the bolt and cone lock together – then further attempts to tighten are going to spin the assembly. One of the problems with the soft Pinns rock is that after you get the bolt to start snugging up, the soft surface under the bolt starts crumbling – or simply crumbles a little from the compressional force of the bolt. You think – oh crap – the hanger is still loose - so you keep trying to tighten it. If you’ve tightened the bolt to the point that the bolt and cone are locked and that causes the surface to crumble a little - then when you try to snug it up again – it just spins – and you think the whole thing is loose.
The torque on these bolts is only 12 foot pounds. That isn’t much.
The installation instructions say to tighten 3 to 4 turns past finger tight.
Do you think maybe we are just overtightening the bolts that spin?
I use a short/mini ratchet handle to try to avoid too much force.
I don’t particularly want to carry a torque wrench but that may be what it comes down to – or at least get one to tighten a few bolts so I can see what 12 foot pounds feels like.

One thing that has always bothered me is the fact that the bolts are labeled as 3/8 (10mm) on the sleeve – it’s stamped right on every bolt. Just for the heck of it I shoved the nose cone fully into the sleeve and at that point the sleeve measures slightly more than a half inch in diameter. I don’t believe that is the design intent but it certainly shows how far the cone could expand in the back of the hole IF the bolt could spin completely through the nose cone - also probably not the design intent since the cone is designed to smash slightly along the slits and lock the bolt (anti-vibration feature). We have speculated at times that spinners might happen when the back of the hole blows out.
The slits in the nose are designed for anti-vibration situations like mounting motors, compressors etc. They are unnecessary for climbing applications in my opinion.
We need a bolt that has a nose cone without the slits.
Once the spinning condition sets in, you may or may not be able to unscrew the bolt from the cone. I have successfully removed several of these spinners and every one of them has a deformed cone that will not allow the bolt to pass through – the bolt and cone locked together as intended by the design.
The easiest and cheapest way to avoid this scenario is to have a solid nose cone.
The other facet I investigated was the installation procedure. Advancing the cone slightly into the sleeve before driving the bolt seems to be a mistake/causes problems.
The Powers installation diagram specifically says not to do it.
Occasionally I have had bolts that are tight immediately after being driven in. I believe this condition is a result of the upper edge of the nose cone catching on the lower edge of the sleeve. When that happens, the nose cone doesn’t go up into the sleeve.
What I have been doing lately is checking to make sure the nose cone advances smoothly into the sleeve prior to driving the bolt. I screw the cone up into the sleeve to make sure it is operating smoothly and then back it off and disengage the cone from the sleeve just before I drive the bolt into the hole. Additionally, I try to be very careful about how the bolt is started. I tap it gently to get the nose cone in the hole and then make sure the bolt is aligned with the hole for the rest of the driving process.
Here are some screenshots from the Powers website.


The Triplex bolts would be a huge improvement over trying to deal with all the finicky intricacies of the 5 piece sleeve bolts and it would eliminate all this speculation and mystery. That bolt combines the best parts of both wedge bolt and sleeve bolt design (one piece stud and solid cone + a single removable sleeve). Simple, strong and elegant – and currently out of stock on the Fixe website. The downside is the bigger hole. One upside is if the hanger becomes loose over time, the bolt can be retightened. I have seen multiple cases of tight 5 pc bolts with loose hangers. Once the bolt and nose cone lock, there is no way to retighten the bolt and get the hanger snug again – unless you try loosening and pounding the bolt in farther – that’s providing the bolt and nose cone aren’t frozen and you’re okay playing with fire. The soft/friable surfaces under the hangers aren’t going away.
